What types of fuel can I use with the DHC2000 torch?
A. Acetylene is the best fuel to use for the majority of applications, particularly when welding and cutting steel. However, any propane-based fuel can be used with the torch. Keep in mind when using a propane based fuel for welding mild steel you will have a very hard and brittle weld – not good for body work. But your Propane based fuels are excellent for cutting and scrapping.
Why is the DHC2000 better than other gas welding torches on the market (e.g. Victor, Harris, Smith, etc.)?
The primary benefit is that the DHC2000 uses 50-60% less fuel and oxygen over conventional gas welding torches. That’s quite an advantage in an economy that has seen dramatic fuel increases over the past decade. Another key benefit lies in the DHC2000’s ability to weld like a TIG and make a clean, concentrated cut similar to that of a plasma cutter –without the added cost.
If fuel costs are such a problem why don’t I go with a MIG or TIG unit?
The short answer is the start-up cost. For even a low grade unit you’re looking at around $500 dollars – quality units can run in the thousands. MIG or TIG systems are useful and they have their place, particularly in industrial applications. However, their size, electrical requirements, and need for a shielding gas make portability difficult or impossible. Dragging them out into the field to repair a tractor, fence, or irrigation pipe can be impractical. Another potential disadvantage of MIG and TIG is that they create what is called a “hard” rather than a “soft” weld. Hard welds, particularly in ferrous (Iron, steel) materials are brittle and more difficult to drill, file or machine. For those of you doing restoration, auto body, metal art will find the soft weld of a oxy/acetylene weld the best for metal forming and shaping.
What does the warranty cover?
The warranty covers only the DHC2000 torch, for the lifetime of the unit.
Will my standard welding hoses fit the DHC2000?
Yes. The DHC2000 connects to a B fitting which is a standard in the welding industry.
Do I need a low pressure regulator set in order to use the DHC2000 torch?
No. If you already have tanks equipped with a standard set of regulators they will work. However, some customers prefer to have the ability to more precisely control the pressure setting – which will optimize the efficiency of the torch.
Where can I see the torch demonstrated in person?
Here you can place an explanation or answer to the question.
Is the DHC2000 torch good at cutting sheet metal?
Yes. The DHC2000 is ideal for cutting sheet steel greater than .010” thick. The low pressure and concentrated flame not only provides for a cleaner cut it also reduces the heat applied to the item being welded, thereby reducing warping of the metal.
How thick of a steel can I cut with the DHC2000?
Applications vary, but generally speaking you can cut commonly used mild steel up to 1” thick.
Can I cut nonferrous (e.g. Aluminum, copper, brass) with the DHC2000?
Yes, to a degree. We call it a melt cut. Using the right technique you can cut nonferrous materials up to 1/16” thick.
How long will the cutting tips last, do they plug easy?
When used properly and with care the cutting tip will last a very long time. As for plugging the cutting tip, this is commonly experienced when welding with conventional cutting torches because molten metal puddles on the surface of the item being cut. The design of the DHC2000 nearly eliminates the surface puddle, thereby reducing the likelihood of plugging the cutting tip.
How thick of a material can I weld with the DHC2000?
Applications vary, but generally speaking the welding range is from .010” to .375” thick, or up to .5” for small applications.
Can I weld stainless or galvanized steel with the DHC2000 torch?
Using what is called a carburized flame you can weld stainless up to 3/8” thick. As far as welding galvanized material goes, it is the same as welding mild steel. Where possible, grind or burn off galvanizing before you start your weld or cut, this will help you from breathing in the gas that comes off the burnt coatings.
What about welding Cast Iron?
Yes. A word of warning though: It is common to see a repair that was done using a nickel-based rod. There are two draw backs to this practice. First, the filler material will not expand and contract at the same rate as the cast iron part – thus allowing cracks to develop at the point of weld. The second is that it is harder to file and machine. For these reasons, we recommend using a 100% pure cast iron filler rod (w/ flux) when welding.
What should I use when repairing cast aluminum?
We have found that using a 4043 TIG filler rod (w/ high temp powdered aluminum flux) is ideal for most applications.
What filler materials can I use when repairing brass or copper items around the house?
Options include: brass/ copper TIG wire; solid copper house wire; and brass brazing rod (after removing the flux coating)
When using the DHC2000, can I weld with propane?
Yes, but only on non-ferrous materials (e.g. Alum.) Welding steel with propane will create a hard or brittle weld that is susceptible to cracking. For this reason, propane-based fuels should not be used for applications involving bodywork.
What pressure do you weld at when using the DHC2000?
All welding is done with both the fuel and the oxygen set at 4psi at the torch (set your regulators 1-2 lbs higher to allow for pressure drop thought your welding hose.) You should always set pressure on regulators in a flow position (torch valve open) and not static (torch valves closed).
Do I need to use flux when welding with all types of filler rod?
No. Flux is only required for welding aluminum and cast iron.
What type of filler rod can I use?
TIG rod is the purest and is commonly available at your local welding supply store.
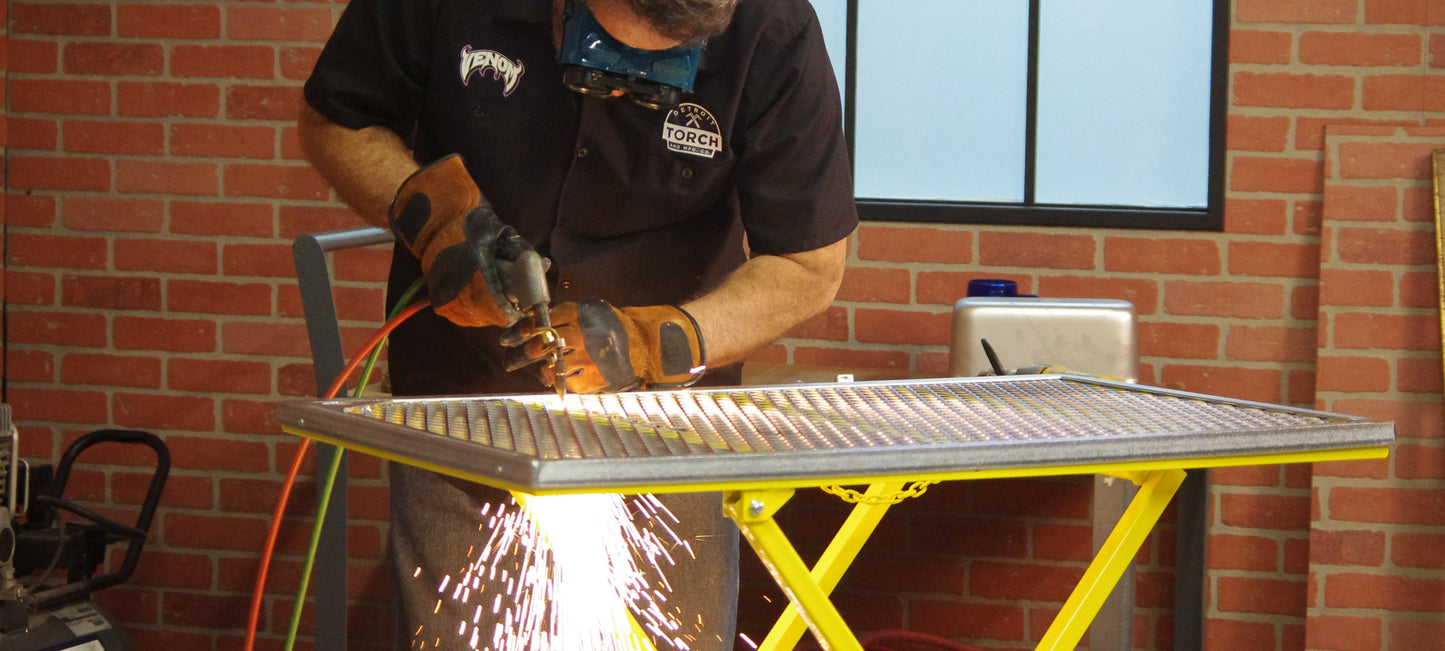
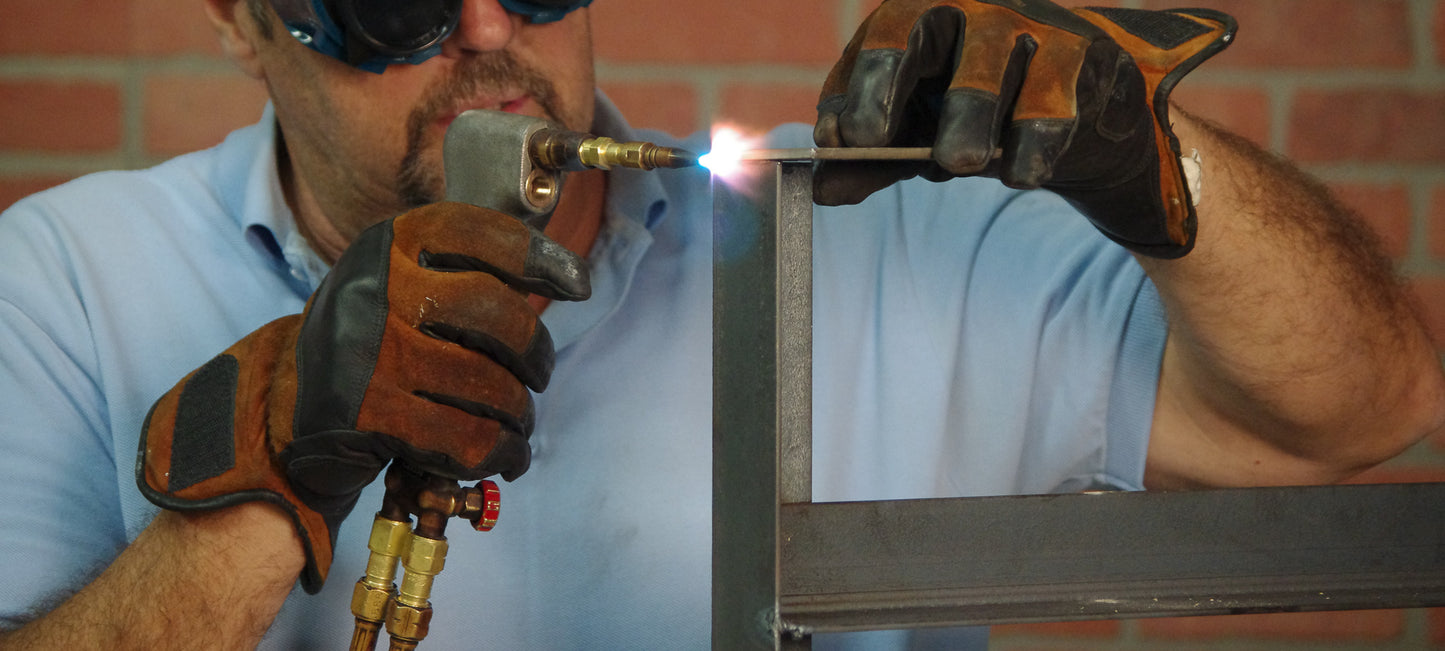